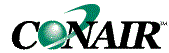
22 Apr 2008
Processors Get Better Control and Save EnergyWith EnergySmart™ Drying System from Conair;Unique Concept Featured at ChinaPlas 2008
The microprocessor-based controls on the EnergySmart™ drying system from Conair give users a detailed picture of the entire drying process, making it possible to optimize settings and produce high-quality finished products more efficiently. At the same time, the unique two-stage drying process actually recycles hot dry air that would otherwise be drained through the system’s return-air heat exchanger. The result is a system that is ideal for PET preform molders and other high-volume users of resins that must be dried at high temperatures. Customers already are reporting energy saving of up to 66% as compared to conventional desiccant dryers. This ingenious approach to drying is being featured in Booth # E3G31 at ChinaPlas 2008, taking place April 17 - 20, 2008, in the Shanghai New International Expo Center in Pudong.
PRECISE CONTROL FOR PROPER DRYING
Energy efficient drying demands that temperature and airflow be controlled exactly to ensure that the resin manufacturer’s specifications are met. In the EnergySmart™ system, the Conair Drying Monitor™ helps provide that precise control. A long probe in the drying hopper extends through the material bed and six integral temperature sensors register the temperature at each position. Data is sent to the EnergySmart™ control, where the temperature profile within the hopper is continuously updated and displayed on the operator screen.
The temperature readings from the Drying Monitor™ are also used to adjust and fine tune the volume of air being delivered to the drying hopper, so that just enough heat energy is added to the bed of material to maintain the optimum temperature profile throughout the hopper. Too much air-flow will result in wasted energy, too little air-flow will result in poor drying performance. The EnergySmart™ drying system controls have the ability to fine-tune the airflow and dewpoint to achieve optimum drying performance.
RECYCLING ENERGY
“When it comes to drying, PET can be a real challenge,” explains Pete Stoughton, Conair PET Sales Manager. “If drying procedures are not meticulously followed and residual moisture remains above 0.005%, the material will undergo a chemical change during melt processing, losing intrinsic viscosity (IV) and physical properties.”
“In a high-volume PET processing operation,” he concludes, “polymer drying is an area where huge energy savings are possible.” Conventional dryers, he says, can consume up to 12% of the total energy consumed in a bottle plant, and up to 25% of the energy consumed in the preform-molding process.
Energy challenges are especially acute in PET drying because the material needs to be dried at very high temperatures. Resin producers recommend that their material be dried in the range of 48 to 177°C (300 to 350°F) for extended periods of time — four to six hours. Raising the temperature of thousands of pounds of resin and holding it at 177°C (350°F) for up to six hours can be very costly. And yet the need for product quality allows for no alternative… until now.
The EnergySmart™ drying system is different because it actually recycles the wasted heat that would otherwise be drained through the drying system’s return-air heat exchanger. In a conventional PET dryer, the air exiting the drying hopper is still quite hot, between 93 - 121°C (200 and 250°F). Because desiccant is much less effective at removing moisture at elevated temperatures, the return air must pass through a heat exchanger where the temperature is reduced to about44°C (120°F). In other words, 27°C (80°F) of heat energy is essentially wasted in a conventional dryer.
That’s why the EnergySmart™ dryer is a “two-stage” system, incorporating a hot-air circuit and a dehumidified-air circuit. In the hot-air circuit, that otherwise-wasted energy is captured. The return air exiting the top of the drying hopper is channeled through a filter and then reheated to 177°C (350°F) before it is re-introduced to the drying hopper through a unique inlet cone located in the middle of the hopper. The Conair system saves energy by not removing heat in the return air heat exchanger and by not having to add as much heat to the air for its next trip through the hopper.
“This recycled air is not quite as dry as normal drying-process air,” explains Pete Stoughton. “Its dew point is between -29 and -18°C (-20 and 0°F) instead of the -40°C (-40°F) resin manufacturers recommend. However, the primary function of the re-circulated hot air in this new system is to pre-heat the polymer in the top half of the hopper to the selected drying temperature. The low moisture level required for PET is achieved in the EnergySmart™ system’s dehumidified circuit.”
DEHUMIDIFIED DRYING
The dehumidified circuit of the EnergySmart™ system incorporates a Conair Carousel Plus™ dryer, which delivers air dried to a -40°C (-40°F) dewpoint and heated to 177°C (350°F), as recommended by PET resin suppliers. Then it is introduced into the drying hopper through an inlet cone at the bottom of the hopper. The hot, dry air rises through the material bed, which has already been preheated in the hot air circuit, maintaining the optimum drying temperature and reducing the moisture content of the material to manufacturer-recommended levels.
“Because we have preheated the PET pellets to the ideal drying temperature in the hot air section of the hopper,” Conair’s Stoughton continues, “we need a considerably smaller volume of desiccated air in the dehumidifying zone. With less air going through the dehumidifying air circuit, we need less energy to heat a smaller volume of air.”
The EnergySmart™ system has other features that enhance efficiency:
•Gas Heat… In high-volume drying applications, gas-fired air heaters are often more cost-efficient than electrical heaters. The new Conair drying system can use either gas or electric fuel.
•Hopper Air Distribution Design… The EnergySmart™ drying hopper utilizes an unique air distribution design. Dual air inlets and a tube-in-tube system are used to introduce hot closed-loop air into the hopper mid-section and hot closed-loop dehumidified air into the lower section of the drying hopper. The dual air inlets are located in the top section of the drying hopper to minimize the impact on mass flow.
•Insulation… To prevent unnecessary heat loss, the hopper and all hot-air ductwork are heavily insulated.
•Carousel Plus™ Technology… The dryers used in the dehumidified-air circuit of the EnergySmart™ system are among the most efficient available. The desiccant-wheel assembly has less structural mass and less desiccant to heat and cool than other dryers.
Reader enquiries
ConairNotes for editors
The Conair Group, Inc. is the world’s leading supplier of auxiliary equipment for plastics processors, including resin drying systems, blenders, feeders and material-conveying systems, temperature-control equipment, granulators and downstream extrusion systems. Seven distinct product lines and 450 individual products solve problems, save energy, cut waste and are easy to use. With long-standing operations in Europe, Asia and South America, Conair is also an international company. Over 500 employees worldwide bring together 50 years of manufacturing experience and youthful creativity to break down barriers to innovation and harness new technology to give customers meaningful, bottom line benefits. The industry’s most complete product line, top-flight engineering and unbeatable service all combine to give processors the confidence they need to succeed in today’s competitive global marketplace.