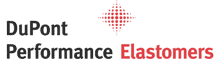
11 Sep 2007
INJECTION MOLDED VITON® FLUOROELASTOMER AND AEM BOND UNIQUELY IN NOLATO FILLER NECK HOSE
Filler neck hoses are key components in the modern automotive fuel system. They must provide a flexible connection between the filler pipe and the fuel tank, strong enough to withstand significant crash impact without fracture and fuel leakage, while providing an impermeable barrier to evaporative emissions in compliance with tough U.S. PZEV and Lev II and European Euro 4 requirements.
Traditional practice was to weld a plastic filler pipe directly onto the fuel tank, but this method is less flexible and the pipe is easily detached at impact. Several hose OEMs overcame the problem by developing extrusion molded rubber hoses, with the inherent no-vibration, interchangeability and adjustability advantages of rubber.
A better way
Nolato Sunne AB , part of the Nolato Group, Sweden, a leading supplier of plastic and rubber products for the automotive industry, devised a better way of manufacturing filler neck hoses to provide flexibility with impressive durability, and fuel permeation resistance to meet Euro 4, Lev II and PZEV evaporative emissions legislation.
The company uses a unique combination of DuPont Performance Elastomers (DPE) Viton® fluoroelastomer (FKM) bonded to ethylene acrylic elastomer (AEM), in an injection molded construction. Jan Bäckström, Director of Marketing and Sales for Nolato Sunne, explains.
“Nolato’s innovative filler neck hose design consist of two layers — an inner layer of Viton® fluoroelastomer which provides an effective barrier to evaporative fuel emissions, and an outer layer of AEM for stability and ozone resistance. The big challenge in succeeding with this unusual concept was to develop an FKM formula that could run smoothly and consistently while being so strong that it could be overmolded with another material without being fully cured.”
“DPE worked closely with Nolato to achieve a degree of FKM + AEM chemical bonding that is quite unique. The bond is so strong that the two materials cannot be separated, to the extent that they can be considered as one layer.”
“Also, as an additional advantage, injection moulding enables various diameters in hose ends, and ribs and locating marks to be designed onto the outer surface for secure clamping and precise assembly — unlike featureless extrusion molded hoses.”
Well proven
Nolato filler neck hose of Viton® and AEM was first commercialized ten years ago, and has been further developed and refined since to meet the latest Euro 4, Lev II and U.S PZEV requirement. Today, the hose is fitted as standard equipment by several leading Tier 1 suppliers for installation in fuel systems for Volvo, Land Rover and Saab models.
Jan Bäckström reports that two additional leading automotive OEMs will shortly adopt the bi-component hoses, with big interest from other OEMs and significant new business potential in the near future. He cites the design freedom of injection molding and the lifetime fuel and permeation resistance of Viton® as keys to its success.
Reader enquiries
Dupont Performance ElastomersChina
(65)6374-8639
emily.lim@dupontelastomers.com
www.dupontelastomers.com
Notes for editors
About DuPont Performance Elastomers
DuPont Performance Elastomers, a global supplier of specialty elastomers with Asia-Pacific headquarters in Singapore, is a wholly owned subsidiary of DuPont. The company is an industry leader in chloroelastomers and fluorinated elastomers, serving the automotive, chemical, petrochemical, semiconductor, food and pharmaceutical processing, construction, general rubber and wire and cable industries.