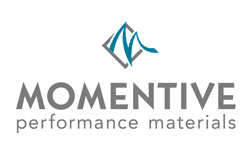
14 Oct 2008
Silicone RTV Technologies for Next Generation Automotive Applications
Author: Egbert Klaassen (Momentive Performance Materials), co-author: Gail Riley (Momentive Performance Materials)
ABSTRACT
Environmental pressures and increasing fuel prices have triggered a number of major developments in the automotive industry. To achieve better fuel economy and emissions control, engineers have been evaluating replacement of mechanical systems with more efficient electronic alternatives. New regulations have provided incentives for industry developments such as hybrid cars, the use of bio-fuel, clean diesel and fuel cell technology. To meet the European directives for "end of life vehicle", design for disassembly and re-use are also increasingly in focus.
Silicone adhesives and encapsulants have been used for many years in tough automotive applications due to their physical property benefits and performance over a wide temperature range. However, several of these new industry developments are resulting in challenging technical requirements for elastomeric materials like adhesives, sealants, and protective coatings. For electronics in particular, new challenges exist in the area of heat dissipation, chemical resistance, and protection for printed circuit boards. In addition, when developing new materials, material regulations such as REACH must be taken into account.
Momentive Performance Materials will present a range of silicone RTV technologies to consider for next generation automotive applications, as well as potentially high productivity solutions for existing applications.
INTRODUCTION: SILICONES A MOST VERSATILE MATERIAL
Silicones are a remarkably versatile family of synthetic materials with hundreds of uses. Silicones are polymers that, depending on the lengths of the chains and the nature of the attached groups, can range from fluids (e.g. used in brake fluids) to resins (e.g. used in wax formulations) to elastomers (e.g. for connector seals). One of the unique characteristics of silicone elastomers is that they provide flexibility over a wide temperature range. This is one of the reasons why silicones are used in many transportation applications where flexibility is required in temperature extremes, such as from summer to winter and over a long period of time.
SILICONE RTV FOR AUTOMOTIVE
Historically, RTV referred to “room temperature vulcanizing” silicone elastomers that consisted of liquid to paste-like viscosities and were applied via a dispensing unit. Today, depending on the catalyst-hydride system, “RTVs” can be cross-linked via condensation or addition cure reactions at room or elevated temperatures. Types of “RTV”s include adhesives, sealants, greases, and encapsulants, including gels, potting materials, and conformal coatings.
The basic chemistry of silicone RTVs provides flexibility, temperature performance, dielectric properties, and durability, a combination that is particularly advantageous in many automotive applications.
The principle structure of the polymer (polyorganosiloxanes) consists of an inorganic Si-O back bone, which provides thermal and oxidative stability, and organic side chains, which provides flexibility without the need for plasticizers.
Figure 1: The Basic Structure of Silicones
The typical benefits of silicone RTVs for Automotive applications are:
• Elasticity without plasticizers
• High temperature resistance up to 200 °C
• Low temperature flexibility down to -60°C
• Dielectric consistency
• Low CTE stress
• Low water absorption
• Weatherability
• Chemical resistance
• Insulation and dampening properties
• Design freedom and processability
Due to these favorable properties, silicone elastomers are used in a wide range of automotive applications ranging from headlamp adhesives to potting materials for electronics protection to LED encapsulation.
Silicone elastomers also have limitations like their steam- and alkali resistance, and the relatively high gas permeability can be a disadvantage in some applications.
HEADLAMPS: A MULTI-FUNCTIONAL SILICONE APPLICATION
Headlamp assemblies provide an excellent application example to show the versatility of silicone. Silicone hardcoat provides scratch and UV protection for the polycarbonate lens, an RTV adhesive may be used for bonding the lens to the housing, and an optically clear silicone may be used for LED chip encapsulation (see figure 2). In addition, LED modules may require a thermal interface material for heat dissipation and an injection moldable silicone can be used for the lens. Headlamp assemblies must withstand temperature and weatherability extremes, making silicone an ideal choice to consider for this application.
Figure 2: Silicone uses in a Headlamp Assembly (illustrative)
ENVIRONMENTAL TRENDS AND NEW APPLICATIONS
The automotive industry today is facing some demanding challenges. Environmental and safety regulations, along with rising fuel costs, are of critical importance. These challenges have accelerated the need for new materials. In particular, the following automotive trends represent opportunities for silicone materials:
DISCUSSION
Low emission, fuel efficiency
Almost all OEMs have programs on alternative powertrain technology and research on utilizing alternative energy sources. For example, hybrid technology utilizes more electronics, which may generate heat that needs to be dissipated for reliable performance. Materials research has been on-going especially in the area of filler technology to improve the thermal conductivity and thermal resistance characteristics of silicone materials. Silicone RTV thermal management materials are typically available in the form of adhesives, greases, or encapsulants. Electronics-based solutions are also being evaluated as replacement of mechanical systems to improve emissions and lower costs.
Figure 3: Illustrative - powertrain concept
More safety and comfort
The challenging demands of new safety regulations help keep engineers innovative. One relatively new safety requirement for the US market is the TREAD Act – Transportation Recall Enhancement, Accountability & Documentation Act. There are many aspects to this legislation. One aspect has been the mandated use of tire pressure monitoring systems (TPMS), which often utilizes sensor technology. Optimum tire pressure not only helps improve driving safety but also helps to achieve better fuel economy. Potential applications for silicone include adhesives to bond sensors to the wheels and potting encapsulants to protect the sensors from the external environment. For this latter application, Momentive developed a new fluoro-RTV potting material, which offers improved chemical resistance over standard RTV potting technology.
Reduced VOCs
The legal and scientific definition of, as well as the regulations surrounding VOCs (Volatile Organic Compounds), is complex and can vary by country. Suffice to say, when selecting materials, low VOC emissions is typically a consideration. There are exceptions, but many solvents are generally classified as VOCs. Many RTV silicones are solvent-free and offer an alternative to solvent-based products. For example, years ago, to achieve a low viscosity RTV conformal coating for printed circuit board protection, dilution with a solvent was a typical solution; today, polymer chemistry is used to achieve a low viscosity coating.
Rising Under-the-hood temperatures
Under-the-hood of an automobile is one of the most demanding environments. From extreme climate conditions to component-generated heat to high thermal and mechanical stresses, under-the-hood of a car puts materials to the test. Space constraints and reduced air-flow are also factors that may contribute to increasing under-the-hood temperatures. One of the benefits of silicone technology is their inherent thermal stability. A typical application for silicone is protection of control modules and electronics located in the engine compartment. For example, in the typical engine or transmission control module, potential applications for RTV silicones include fast curing lid seal adhesives, low modulus potting gels, low viscosity conformal coatings for PCB protection, and thermally conductive adhesives for heat dissipation.
Increasing cost pressures
Cost pressure is a way of life in the automotive industry. Productivity from reduced cycle times is often a key factor in material selection. Silicone RTV technology offers a range of cure options, from room temperature cure adhesives with fast green strength to elevated-heat cure chemistries with quick, complete cure.
In addition, new developments in addition cure adhesive chemistry allows for lower temperature-heat cure options, which may lower energy consumption. It is also an advantage as many electronics contain sensitive components that cannot withstand the elevated heat required of traditional addition cure systems.
Design for disassembly
Silicones durability in extreme environments may contribute to longer part life through improved part reliability, thereby reducing costs and the need for spare part materials manufacturing. In certain electronics applications, increasing demands towards design-for-disassembly and re-use have triggered developments around easy to remove silicones, such as thermally conductive silicone grease and gels. Where applications require part removability, these products may be considered as alternatives to the more permanent adhesive technology.
CONCLUSION
The recent trends in the automotive industry are providing challenging opportunities for material development companies. Environmental pressures, safety legislations, and increasing fuel prices are just some of today’s challenges. The versatility of silicone chemistry and their inherent properties often make them ideal materials to consider for many applications. Momentive Performance Materials is a premier silicones materials supplier with a range of RTV technologies to consider for next generation automotive applications.
Reader enquiries
Momentive Performance MaterialsChempark Leverkusen
51368 Leverkusen
Germany
Central European Customer Service: cs-eur.silicones@momentive.com
Toll free telephone: 0080043211000
+31 (0) 164 225 350
www.momentive.com
Notes for editors
About Momentive Performance Materials
Momentive Performance Materials Inc. is a premier specialty materials company, providing high-technology materials solutions to the silicones, quartz and ceramics markets. The company, as a global leader with worldwide operations, has a robust product portfolio, an enduring tradition of service excellence, and industry-leading research and development capabilities. Momentive Performance Materials Inc. is controlled by an affiliate of Apollo Management, L.P. Additional information is available at www.momentive.com.
*Invisisil and Snapsil are trademarks of Momentive Performance Materials Inc.
Related images