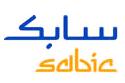
19 May 2023
在电动汽车充电站中用塑料代替金属,助力改进生产、安装和操作流程
在向电动汽车 (EV) 过渡的过程中,高效可靠且随处可见的基础充电设施是其中一项关键因素。人们希望能轻松地找到附近的公共充电站并快速地为车辆充电。而目前电动汽车充电桩并非随处可见。尤其是在乡村地区,充电桩要么无法使用,要么充电时间过长。
截至2022年底,全球约有230万个电动汽车充电站,其中65%在中国。其中广东省拥有最多的充电站(截至 2022 年 9 月底,共有 345,126 个公共充电桩和 19,116 个充电站)。根据国家发改委与国务院九部委1月联合印发的一份文件,到 2025 年,中国政府计划将建成能够满足超过2000万辆电动汽车充电需求的充电基础设施体系。在欧洲国家中,荷兰拥有最多的充电站,其次是法国、德国和英国。由于各国积极投资于充电基础设施的建设,尤其是能够向电动汽车提供直流电(相对于交流电而言)以节省充电时间的快充技术,充电站数量保持持续增长的态势。
如今,随着高效可靠的基础充电设施实现广泛布局,如何选材在加速生产,便于安装和改善充电桩可靠性等方面扮演重要的角色。通过将具有特殊性能的塑料材料取代目前应用于多种电动汽车充电系统部件中的金属材料,可以有效降低成本、提高生产效率并减少碳足迹。
与金属相比,塑料能够实现部件整合和功能集成并且外表美观,它可以提供更大的设计自由度。塑料材料有助于精简生产流程,并可通过应用高速率、大批量注塑成型生产工艺、省去抛光和喷漆等二次操作步骤来降低成本。重量方面,塑料比金属更轻,能提高充电设备运输的能源效率、简化设备安装流程。由于塑料具有高抗冲击性、耐候性、耐化学性和耐紫外线性以及阻燃性 (FR) 等特殊性能,有助于提升安全性和可靠性,同时延长充电器使用寿命(具体取决于充电设备不同部件的技术规格要求)。
面向电动汽车充电器应用领域推出的塑料解决方案
充电装置的外壳和室外馈线柜可采由阻燃聚碳酸酯 (PC) 或 PC 与聚对苯二甲酸丁二醇酯 (PBT) 的混合物模制而成。例如,SABIC 的 LEXAN™ PC 树脂可进行模内着色,而且具有良好的表面外观、高冲击强度以及良好的阻燃性能,有助于增强美观性和安全性。
内板、室内和室外充电桩均可采用 PC 和丙烯腈-丁二烯-苯乙烯 (ABS) 的阻燃混合物生产,成品可提供良好的尺寸稳定性和高抗冲击性。除了可以替代金属外,薄壁设计且有阻燃性能的塑料方案可以进一步减轻重量,同时预留更多空间安装其他组件。
对于车身框架和缓冲块等结构部件,长玻纤增强聚丙烯 (PP) 化合物(如 STAMAX™ 树脂)具有高强度、高刚度和耐冲击性等特性,有助于提升使用寿命,且能够在单个部件中集成多种功能。
应用于显示屏和光导的透明光学级 PC具有多项优势,包括抗冲击性能和耐高/低温性能。此类树脂可进行硬质涂层以提高耐磨性。这一点对于触摸屏而言非常重要。
前侧充电枪托、充电连接器、插头和耦合器等部件的制造需要采用具有良好电气性能的材料。阻燃 PBT 材料或 PC/PBT 混合物可提供较高的相比漏电起痕指数 (CTI)、良好的耐化学性和低吸水性。
电动汽车充电器制造商可从中获益
在电动汽车充电应用中,采用塑料替代金属可以为制造商提供多种优势,例如,降低成本、改善外观和提升可持续性等。与金属相比,塑料能够提供更大的设计自由度,易于打造各种复杂的几何形状,同步实现零件加工和功能集成。由于塑料具有良好的延展性,可以为充电器外壳打造出色的外观效果。在成型过程中,塑料还可以为成品赋予不同的表面光洁度和纹理(例如,高光、哑光和鹅卵石纹等)。标志和文字也可以通过模内成型、浮雕或激光雕刻等工艺与塑料件实现一体成型。此外,塑料还可以提供高透光、半透明到不透明等透明度加工选择。
与金属相比,塑料可以实现更精简的生产流程和更高效的组装操作。高速率、大批量注塑成型生产工艺缩短了周期时间,而包覆成型或双射(2K)成型则可以将两种操作合二为一。使用具有标准或定制模内颜色的塑料牌号代替喷漆工艺,有助于进一步简化生产,同时可以避免暴露于挥发性污染物排放的环境中。
通过应用生物基材料或含有回收成分的再生产品等可持续材料,塑料供应商继续拓宽其产品组合。此类材料的使用有助于推动汽车电气化走向更可持续的未来。
结合 BLUEHERO™品牌丰富的专业知识,SABIC推出了全塑设计的充电桩概念展品,以展示高性能塑料树脂和混合塑料在电动汽车充电器中的使用。根据BLUEHERO 计划,SABIC全力帮助世界能源加速向电力的过渡,同时为实现全球气候变化目标提供支持。
读者查询
New ItemRelated images